top of page
770-534-3681
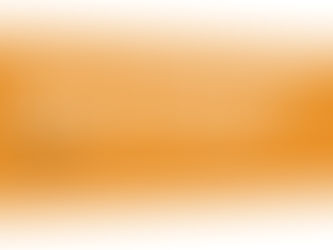
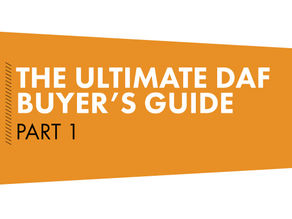
Part 1: The Ultimate DAF System Buyer's Guide
At a certain point in the project development process you will have qualified a few dissolved air flotation (DAF) system manufacturers...
5 min read

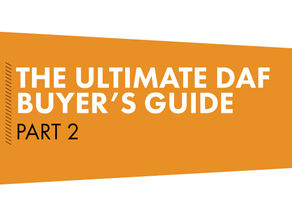
Part 2: The Ultimate DAF System Buyer's Guide
When you buy a DAF system, you want something that is going to hold up in a harsh environment.
4 min read

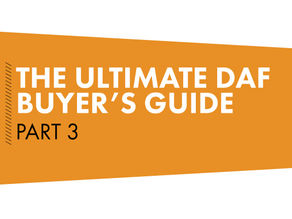
Part 3: The Ultimate DAF System Buyer's Guide
The method used to distribute whitewater into the incoming wastewater stream makes all the difference in the way sludge forms and floats...
3 min read
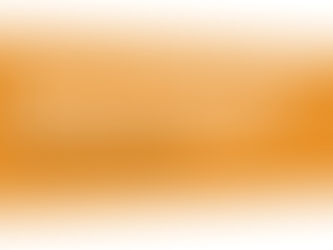

Conclusion: The Ultimate DAF System Buyer's Guide
At face value DAF systems are pretty much like any other piece of industrial equipment – they’re an investment that you only want to make...
2 min read

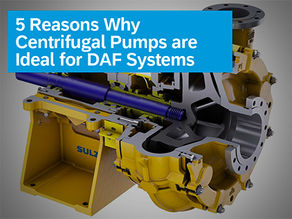
5 Reasons Why Centrifugal Pumps are Ideal for DAF Systems
DAF pumps are the key component of all DAF Systems. On it rides some of the largest capital, operations and maintenance expenses involved...
2 min read

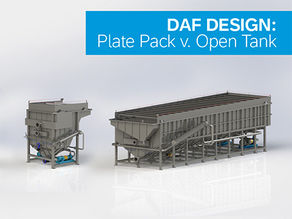
DAF System Design | Plate Pack vs. Open Tank
At FRC, we offer two primary Dissolved Air Flotation (DAF) system designs: the Plate Pack or High Rate DAF System and the Open Style DAF...
4 min read


5 Reasons Operators Prefer FRC Systems DAF Design
What is it about FRC Systems DAF design that makes wastewater operators jobs so much better?
2 min read

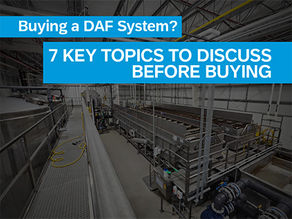
Buying a DAF System? 7 Key Topics to Discuss Before Deciding
There are a lot of companies out there that will sell you anything they think you might need.
3 min read


Be Prepared for the Unexpected: The Importance of Keeping Spare Parts
Preparation is key to minimizing downtime and maintaining the efficiency of your Dissolved Air Flotation (DAF) system. At FRC, we’ve...
2 min read
bottom of page